New method for advanced aluminium welding
– Published 4 July 2014
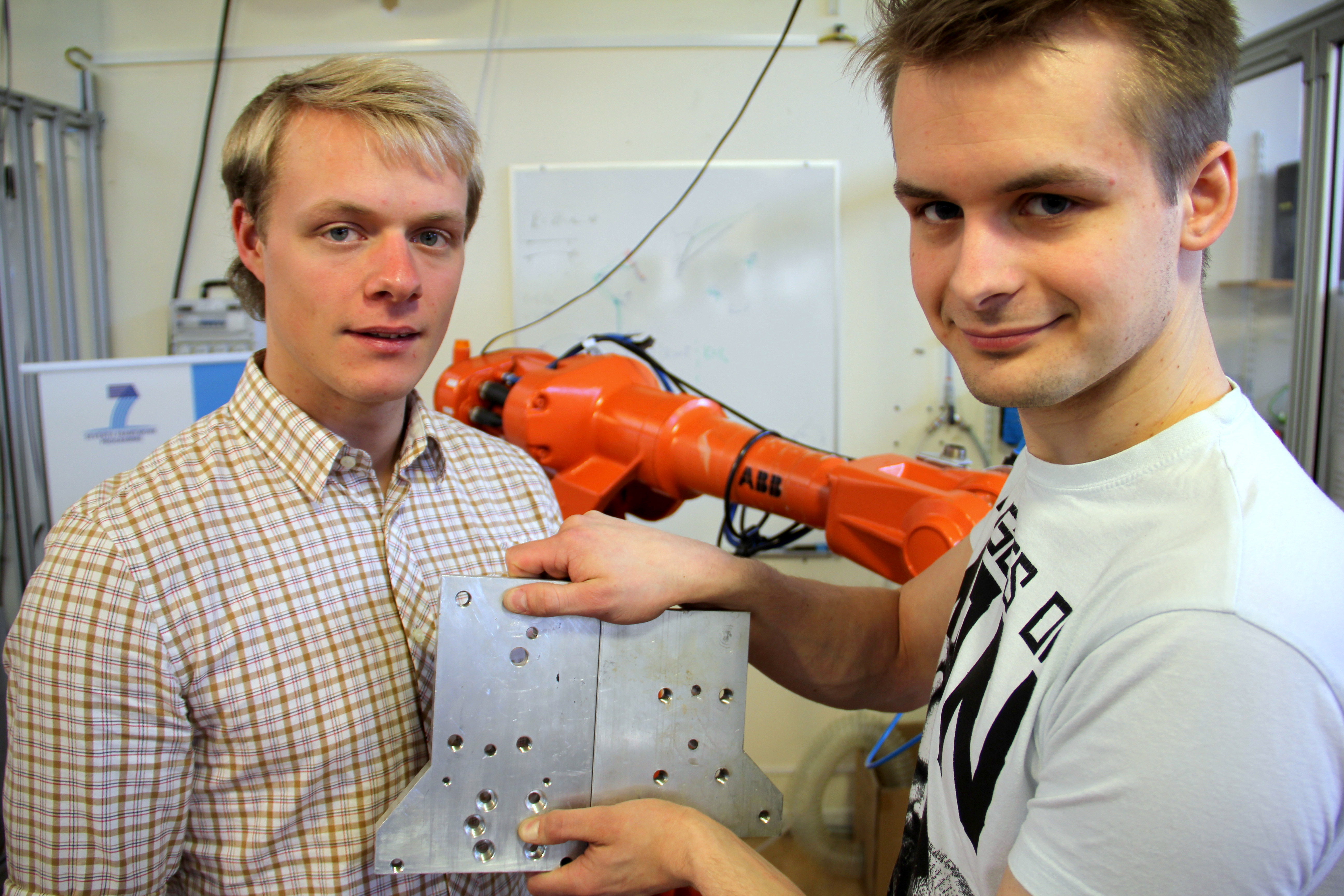
Aluminium is a lightweight material which is suitable for use in everything from cars to boats and planes. However, one of the problems of this material is that it is hard to join, as traditional welding, for example, does not work. Now researchers from the Departments of Automatic Control and Computer Science at LTH are taking part in the joint European project, FlexiFab, which is developing a system for friction welding with industrial robots.
The aim is to enable the system to join parts of complex structures with high precision and to facilitate the use of aluminium constructions in the European transport sector.
When two metal plates are fastened together, a conical friction tool is used to loosen material from one plate and mix it with material from the other, and vice versa. Thus the metal heats up, but not to the extent that it melts. The procedure can be compared with a mechanical mixing; this entails the seam between the plates being filled in, which in turn fastens the plates together.
Friction welding has so far required very strong processing power, but a new method developed by a project partner, TWI, the first to develop friction welding in the early 90s, has opened up new opportunities to use industrial robots instead of large and expensive specialised machinery.
Using relatively pliable robots does, however, make high demands on automatic control in order to achieve the precision required; it is mainly on this aspect that LTH will focus its efforts.
”The project will eventually enable even difficult aluminium alloys to be joined more effectively and cheaply than today. This facilitates the use of light constructions within the transport sector which in turn reduces fuel consumption. The project is also to enable welders to have a more favourable work environment”, says Anders Robertsson, professor at the Department of Automatic Control at LTH.
The project consortium consists of eleven different agents and is coordinated by the European welding federation, EWF.
Anders Frick